Recently during a standard review of one of our customer’s purchase orders, we noticed that one of the lot numbers on the order was the same lot number that we marked on the parts for the previous order. We stopped the set-up process and contacted the customer to make sure that the lot number was correct before proceeding with the order. The customer informed us that the lot number on the PO was incorrect and gave us the correct lot number to mark onto the parts. Needless to say, they were very happy that we caught this error. Our ability to catch this error saved them a lot of time, money and the effort of reworking this entire lot of parts.
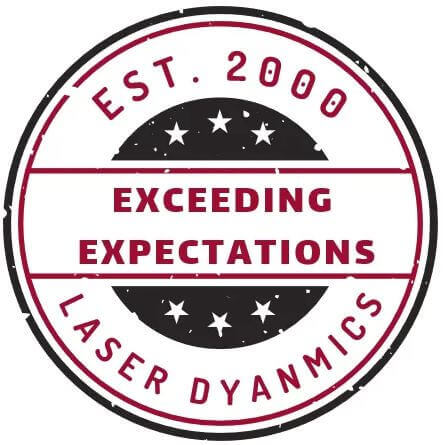
This is an example of the level of quality that our customers have come to expect and enjoy when working with us. In our ISO Quality Management System, one of the things that we track and review constantly is our customer paperwork accuracy. Paperwork errors can sometimes seem small at the time, but multiple errors can quickly add up to a significant amount of wasted time for both the customer and the supplier.
Not only do we strive to exceed our customers’ expectations on the quality of parts that we provide to our customers, we also strive for accuracy throughout the entire process. Whether it be paperwork or packaging we are dedicated to achieving excellence in each and every job that we do.
LASER DYNAMICS, INC.
Laser processing is a basic need for most companies. Whether you’re searching for identifying your product with permanent logos, mass-producing identical parts through precise laser cutting, or hermetically welding two workpieces together, the upfront price of the lasers and training is costly to both finances and time. Laser Dynamics provides the expertise, fast turn-around time, and top-of-the-line lasers to ensure that your product not only functions as intended but looks great!